Industrial IoT in Manufacturing: Major Pains for a CTO to Address
July 12, 2023
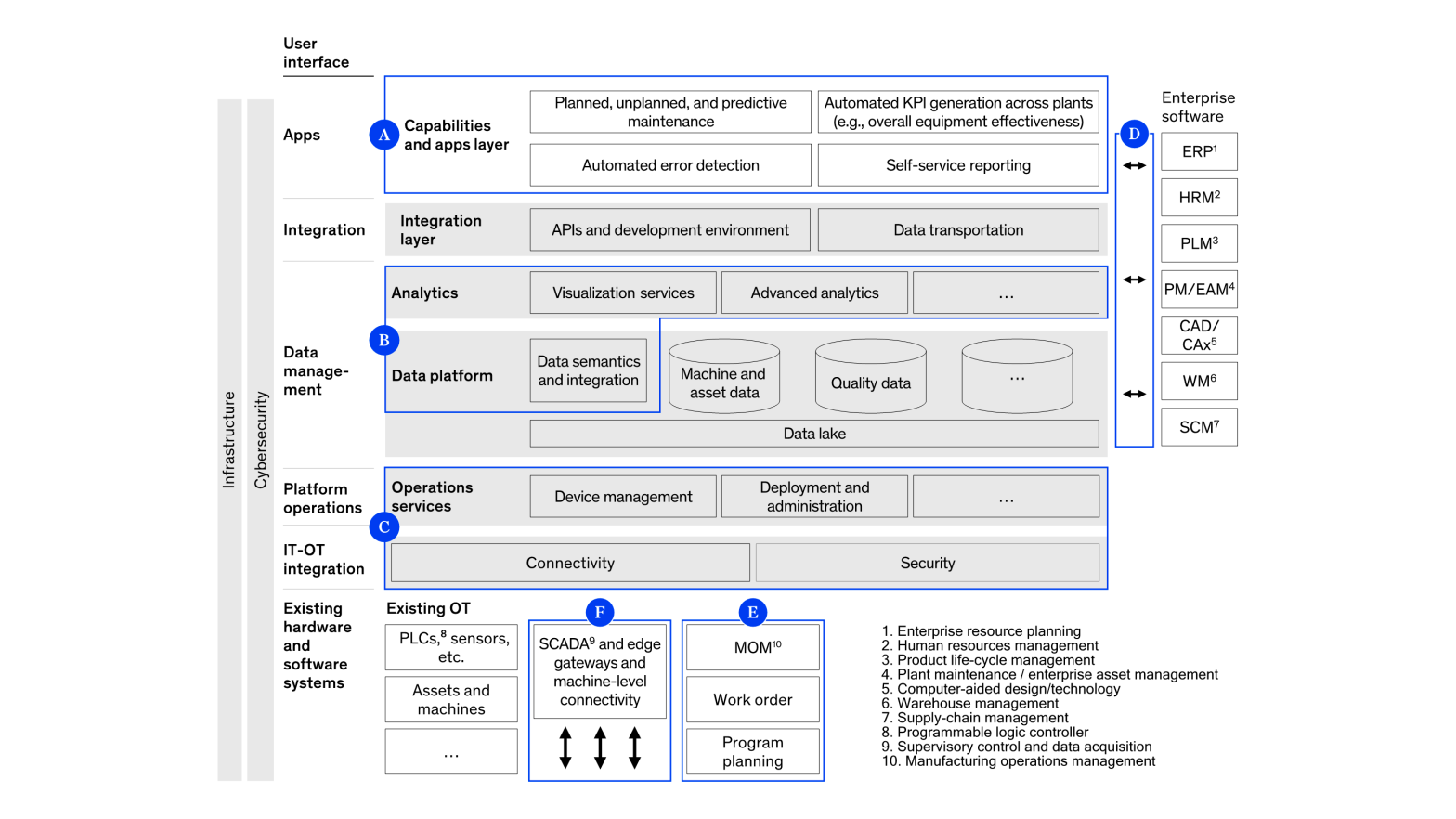
Aiming for operational improvements, manufacturers are struggling with system complexities. Is there a way out?
IIoT projects do not scale beyond pilots
Manufacturers rely on the industrial Internet of Things (IIoT) to monitor equipment performance, oversee production output, track energy consumption, etc. As a result, this helps to identify bottlenecks and implement optimization strategies to improve safety, productivity, and efficiency.
A 2021 study by IBM mentioned IIoT as one of the four key technologies to help manufacturers in their digital transformation journey. On the other hand, another report by McKinsey highlighted that 70% of manufacturers surveyed could not scale IoT beyond pilots. Furthermore, a 2022 study by Bain & Company found that four-fifths of companies are scaling fewer than 60% of IIoT proofs of concept. Though Microsoft and IoT Analytics recently found out that the situation improved by 2023, it is still far from perfect.
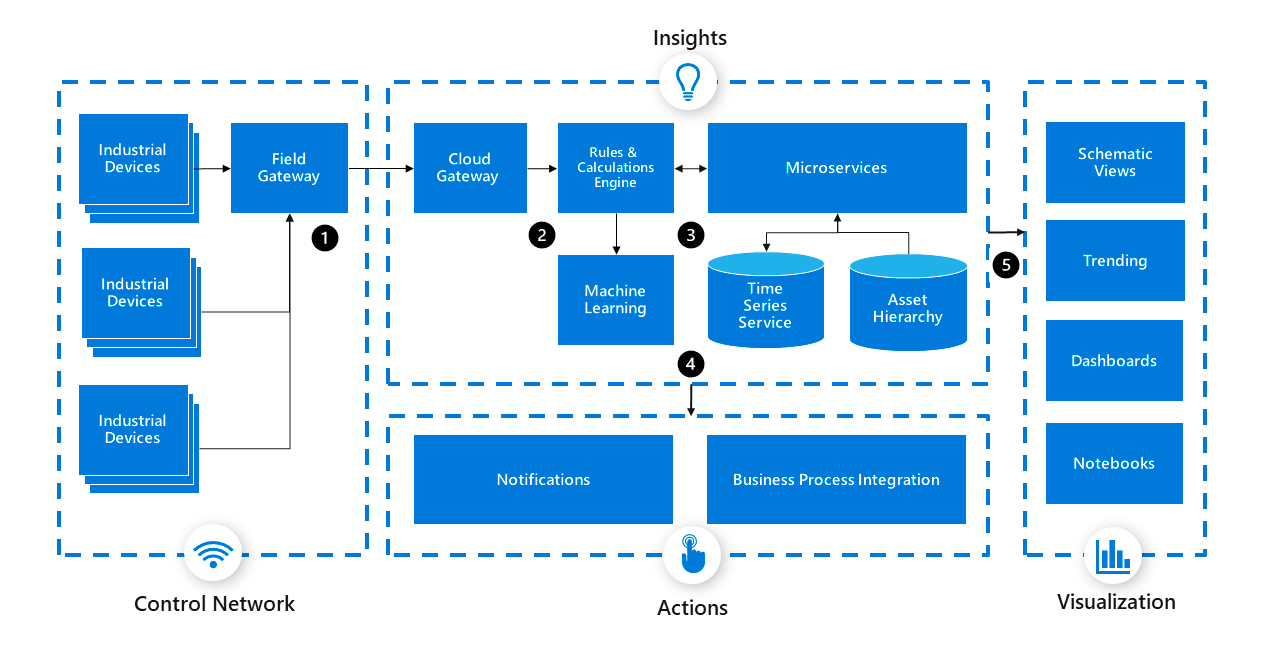
What makes the industrial Internet of Things in manufacturing so complex to implement and scale? This article examines IoT’s major scenarios and adoption barriers in manufacturing, along with some best practices and guidelines to follow.
Top IIoT scenarios in manufacturing
Companies are exploring IIoT opportunities for various reasons. According to Microsoft’s report (August 2022), the primary goals for deploying Industrial IoT are associated with operational improvements. In this regard, 86% of manufacturers consider equipment effectiveness the most important criterion—along with optimization of production output/quality, enhanced employee efficiency, or decreased costs.
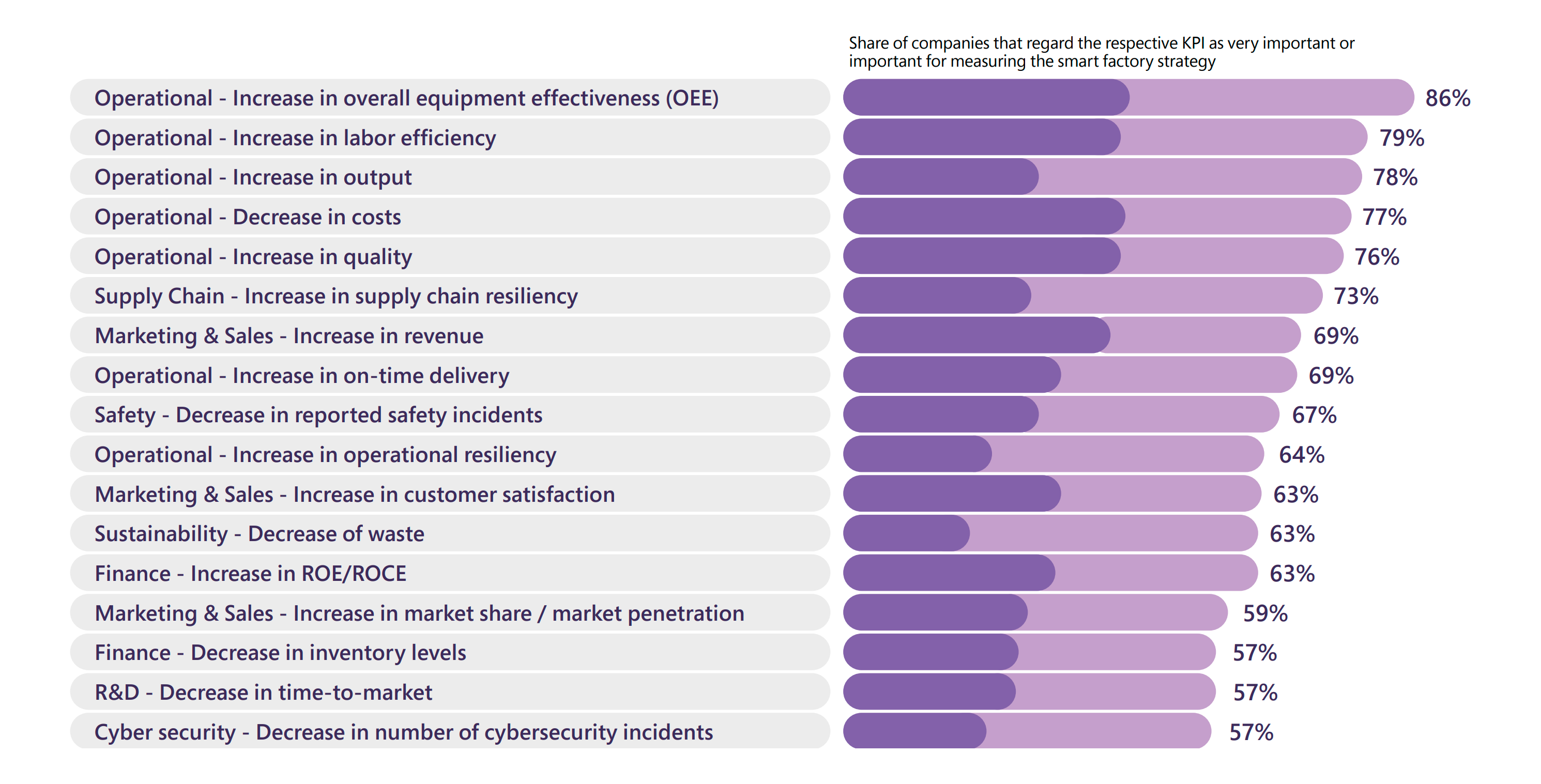
McKinsey, too, describes the optimization of industrial operations as the use case with the highest potential economic value (November 2021). Another survey by HiveMQ and IIoT World defined increased productivity and improved equipment effectiveness as the top benefits companies expect to gain from implementing industrial IoT systems (October 2022).
In addition to real-time monitoring of equipment conditions (such as temperature or vibrations), industrial sensors can enable condition-based or predictive maintenance. During this process, machine learning can be utilized to detect anomalies and take actions based on the telemetry data. By utilizing event-driven architectures, the system can trigger an alert, such as recommending maintenance operations, before a failure actually occurs. As a result, this can ensure a safer working environment and lower repair costs.
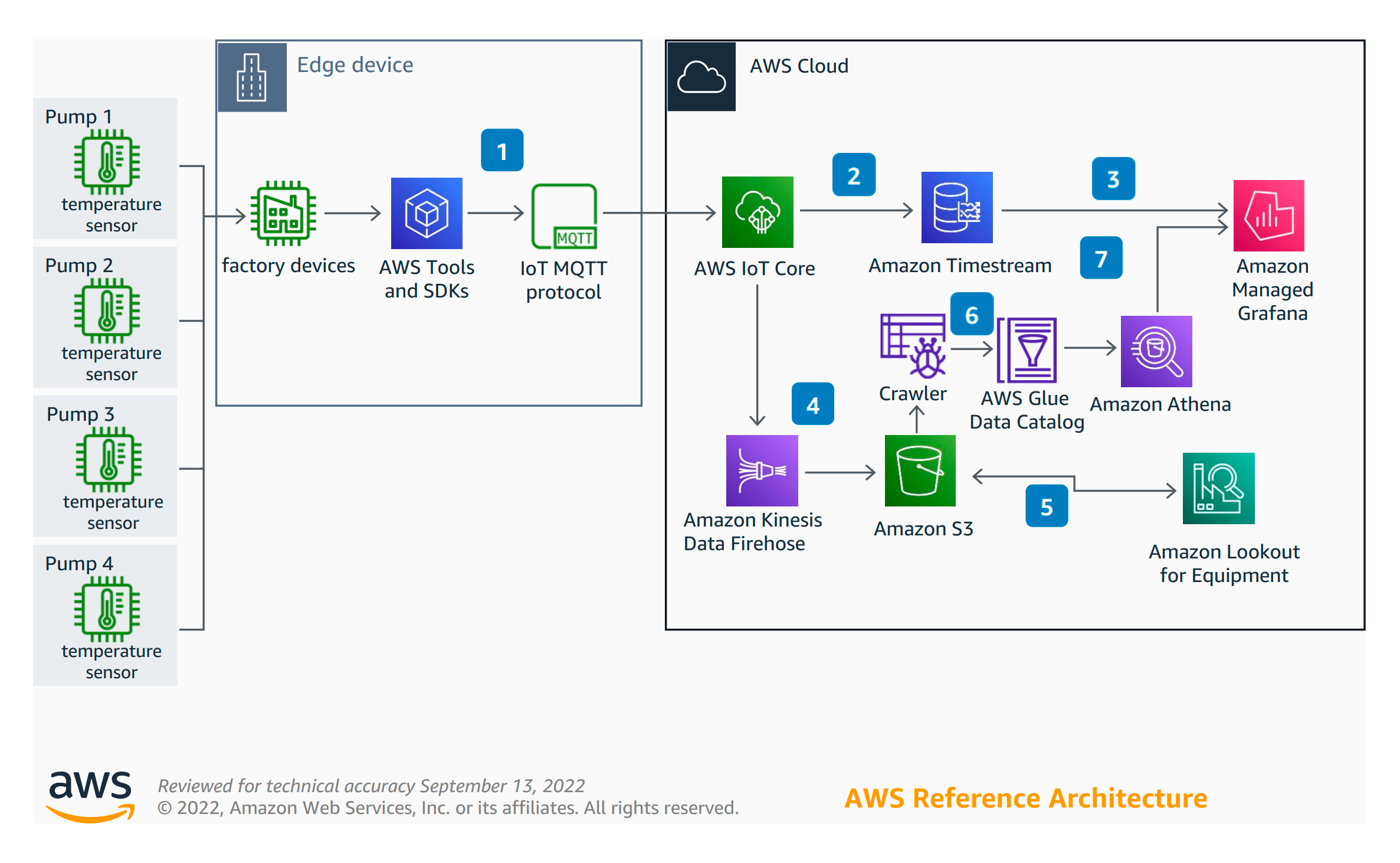
A manufacturer can also monitor equipment’s energy consumption through a network of smart meters deployed across the plant. This allows to improve or predict consumption patterns and peak loads—optimizing energy procurement and distribution. In 2021, McKinsey found that IoT implementation helped organizations enhance energy efficiency by up to 50% in some cases.
In manufacturing, the industrial Internet of Things can also be used to monitor the current location of numerous assets distributed across warehouses. According to Microsoft, inventory management and location tracking are among top 3 use cases for smart products that manufacturers deliver to the market—along with monitoring dashboards. To implement this goal, IIoT can engage radio-frequency identification (RFID) tools. This technology enables manufacturers to label their inventory items with a tag containing essential data. Then, it is possible to track the location or flow of assets via multiple RFID readers connected to an IoT system (like GE did here).
Some companies also aim at building digital twins, which should act as virtual copies of a factory, equipment, or a product. It is a representation of the key assets and workflows used by manufacturers for simulation, supervision, and testing of industrial objects. The role of IIoT here is to connect the plant (or equipment) to its digital counterpart, collecting telemetry in real time and translating it into virtual representations. Despite the benefits, Microsoft reports that digital twins are still not so widespread—due to a combination of technical complexities, integration challenges, cost, etc. “The focus is more on a specific subsystem or scope within the factory,” Dr. Emile Glorieux of Coventry’s Manufacturing Technology Centre stated in a 2022 interview. Dr. Glorieux attributes this to “a trade-off between the costs and benefits you get from the digital twin.”
Main IIoT adoption challenges
Implementing and scaling IIoT in manufacturing is a rewarding, but a challenging journey, encompassing both technology and organizational aspects.
1. Legacy systems and disintegration
Bain & Company names the complexity of integration the main barrier to scaling IIoT proofs of concept (September 2022). The layered architecture of an IIoT environment inevitably includes different types of software and hardware—hundreds or even thousands of apps and devices. 42% of respondents in Microsoft’s report consider interfacing with existing applications to be a challenge (August 2022).
The problem is aggravated by numerous components or devices relying on different network protocols/standards. In particular, HiveMQ reports that HTTP (55%), MQTT (48%), Modbus (41%), and OPC Unified Architecture (33%) represent the most common protocols for connecting equipment (October 2022). The results of the survey demonstrate that manufacturers often use several different protocols at a time.
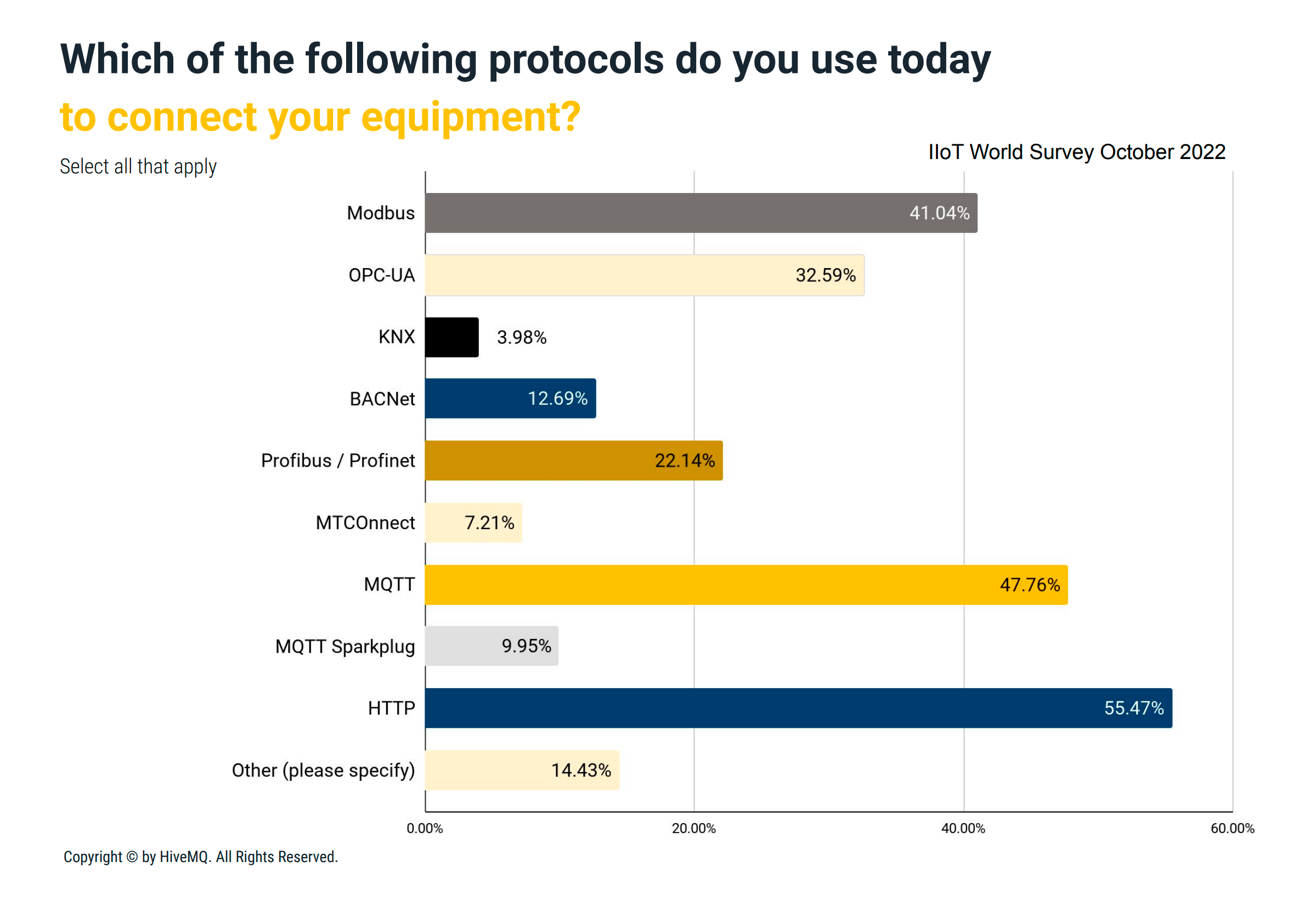
This issue is further amplified by legacy systems/tools/devices utilizing outdated technologies. According to ISG’s survey (May 2023), US-based companies highlighted legacy equipment as the second biggest challenge of their smart manufacturing programs—following change management.
Having this issue ignored, organizations risk creating information silos or facing data consistency issues. Therefore, in an aim to bridge the systems, manufacturers try to integrate myriads of software and devices via application programming interfaces (APIs), if the latter are delivered out-of-the-box. If not, companies spend months developing APIs and brokers from scratch or finding other ways to transfer signals and information between equipment, production line, BI/ERP modules, etc.
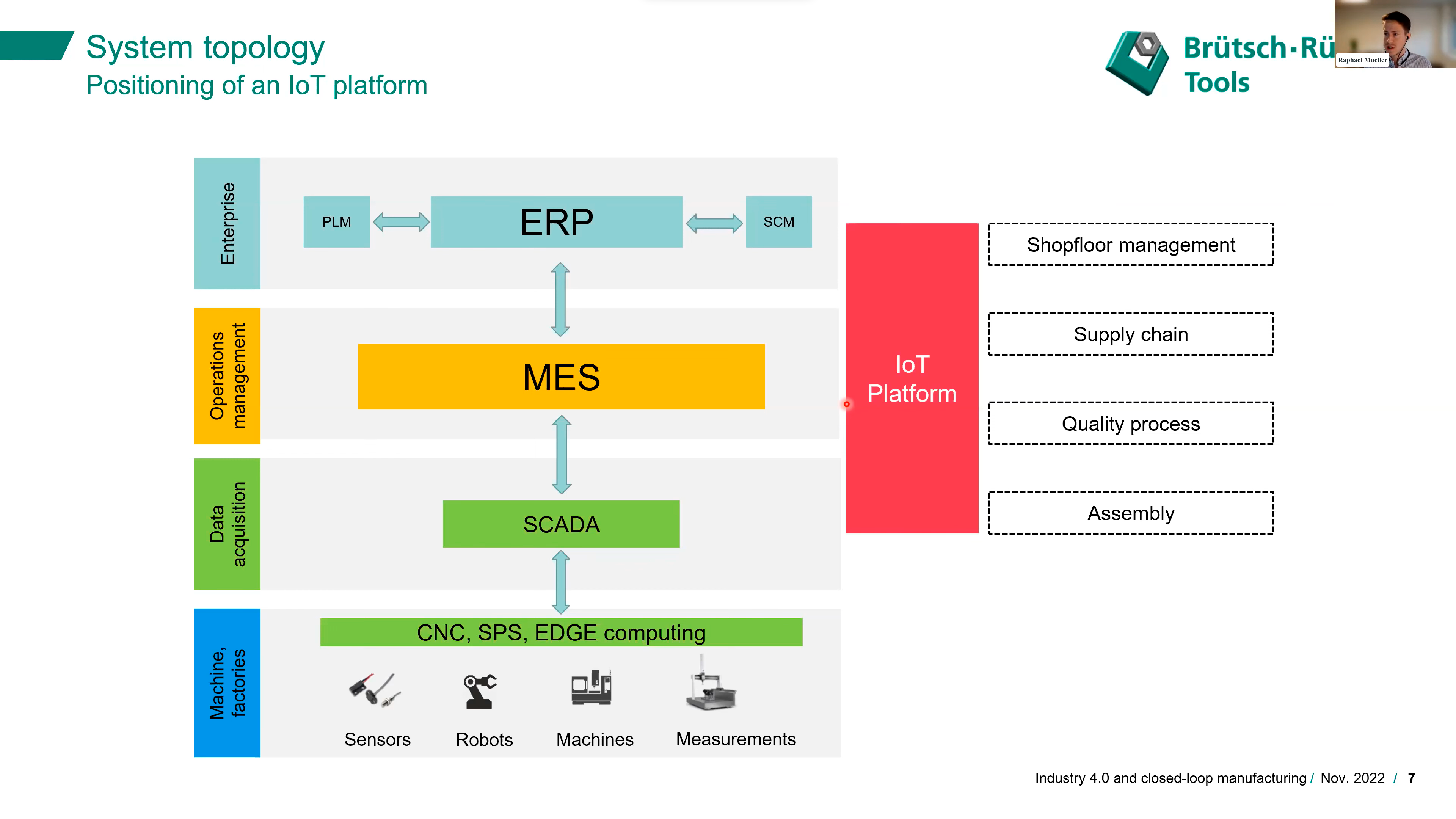
(For instance, a roof truss manufacturer we worked with needed to integrate its existing CAD system with the robotics management software to identify defective elements. To take them off the production line as early as possible, the company transferred the information about the design of the products to the assembly line in real time via APIs. Once a defective item was detected, the platform sent signals to the robotics software, introducing changes to the assembly process on the go. The company spent several months transforming a rough POC into a production-ready management system.)
To facilitate integration among such components, McKinsey recommends taking into account the following initiatives:
- Protocol standardization. On the one hand, early adoption of IIoT devices sharing the same communication protocols can simplify integration. On the other hand, in reality, we will deal with legacy IoT devices sooner or later, making it necessary to create an Enterprise Service Bus (ESB) or its analogue at some point. This architecture represents a centralized middleware to convert different communication protocols, connecting legacy devices via customized adapters. McKinsey also highlights that a focus should be “placed on having correctly labeled data (especially time stamps) to make use of data.”
- API development. McKinsey emphasizes microservices (below) and APIs as “the key to developing a technical platform capable of supporting the level of flexibility and agility needed.” APIs can be created from scratch and may involve the adoption of tools that automate the development. (Turning to a trusted partner may also help.)
- Microservices. Integrating and scaling complex IIoT systems requires continuous changes and upgrades. However, ongoing maintenance can disrupt a monolithic system as well as the processes relying on it. As a response to this challenge, microservices can replace typical rigid architectures with modular, loosely coupled units that work independently without affecting the other components. One of the ways to amplify the ease of integration and scalability ensured by microservices is implementing the serverless model. Here, a cloud provider takes care of the underlying infrastructure on which a particular microservice/function runs, reducing operational efforts.
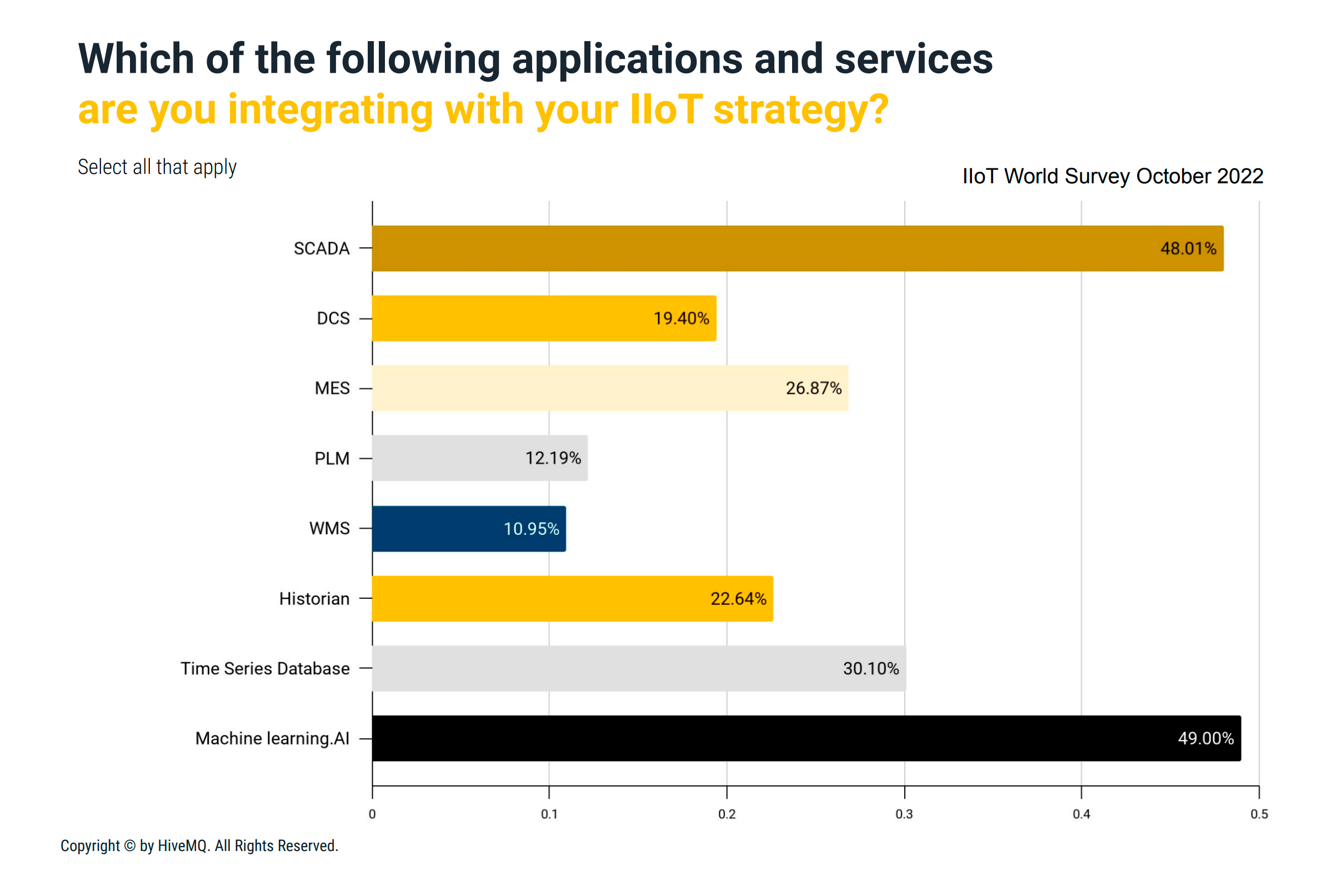
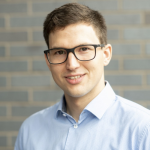
“In manufacturing, it’s always a challenge to retrofit new technologies on pieces of legacy equipment in an existing factory…It can be very costly to install new sensors. Especially when the production system is in operation, it’s very costly to interrupt operation, install some sensors, commission the controls. And so, the benefits…need to justify the cost of having to do that work.” —Dr. Emile Glorieux
2. Data management
Manufacturers scaling IIoT may struggle to handle data due to its volume and complexity. These two parameters refer to the presence of huge data sets with their own native formats and flowing from disparate sources. For example, an ABB survey reveals that 22% of automotive manufacturers are concerned about data management. Besides, Microsoft’s 2023 report shows that 20% of IoT projects struggle with utilizing data efficiently.
At the recent All Things IIoT Day, Charles Chatt (Engineering Leader at Hitachi Vantara) shared his thoughts on the issue.
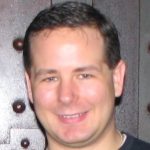
“Data lakes turn into data swamps, because you’ve got that [information] in its raw format, and it’s unrefined. You’re putting it in because that has incredible value to folks like data scientists who really want to dig in there. Unfortunately, absent [is] the context. Understanding what is there, understanding how to use it becomes difficult.” —Charles Chatt
To properly store and analyze this information, an IIoT system will need a suitable data platform. The implementation should be able to easily scale, manage time-series data, and support flexible schemas (the way information is organized within the database). Here are a few options mentioned by McKinsey and Amazon that can contribute to efficient data processing:
- NoSQL databases. While SQL databases store information based on well-defined schemas, their NoSQL counterparts organize data into more flexible structures. This enables NoSQL databases to store complex formats, such as unstructured data, making them ideal when scaling IIoT across multiple use cases, as pointed out by Microsoft.
- Databases as a service (DBaaS). It is a licensing and delivery model in which a cloud provider offers highly scalable storage and computing resources on demand. Manufacturers prioritizing scalability for their IIoT solution may find DBaaS a very cost-efficient option.
- Time-series databases. These are optimized to store and query time-series data, which is a very common data type in manufacturing scenarios (for example, temperature trends in industrial machinery).
- Data warehouses. It is a type of an enterprise system designed to unify the most critical information from multiple sources for data querying, consistency, and other purposes. This architecture involves ETL (extract, transform, and load) and data quality processes, and may become a key component in business intelligence.
- Data lakes. Unlike data warehouses, these systems have no strict requirements in terms of data formats to ingest. They can store structured data for analytics, but can also be used as cheap repositories to keep unstructured information that might be useful in the future. (This reference card from Amazon may be helpful.)
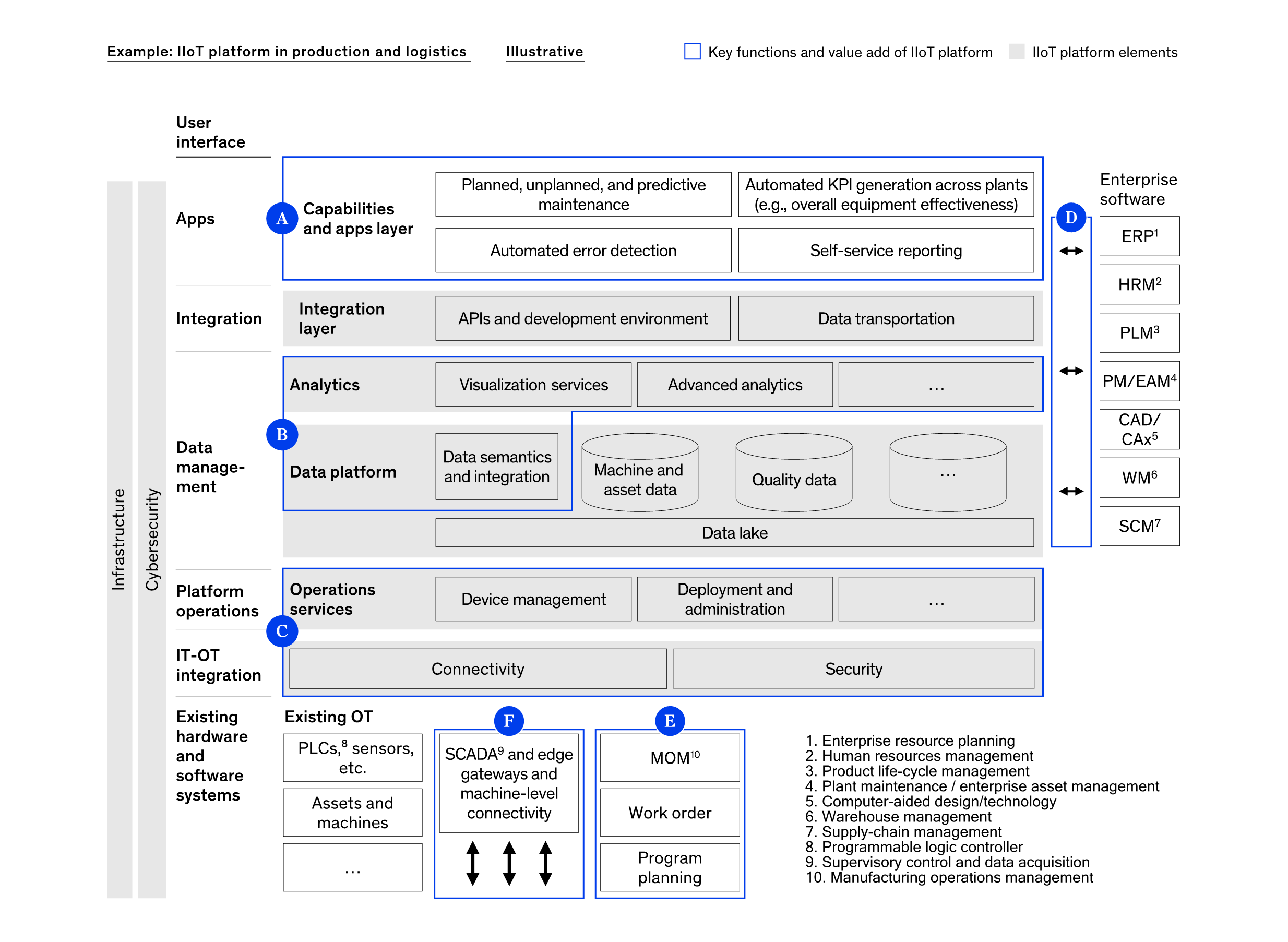
McKinsey also names edge computing one of the most efficient approaches to help with managing large volumes of real-time IoT data. By minimizing the physical distance between a data source (e.g., machinery) and the computing power, latency reduces, and the IoT system can portray production processes faster. On the other hand, maintaining or updating software on the edge can be quite hard, and may require specific techniques, such as containerization.
3. Security
IIoT platforms can have several points of vulnerability due to the reliance on remote connections and the multitude of integrated devices. Furthermore, legacy systems are usually more prone to risk. In April 2023, 32% of respondents of McKinsey’s survey named cybersecurity the top obstacle to IoT adoption. In a report by HiveMQ and IIoT World, 39% of companies cited cybersecurity as one of the key challenges to implementing a new IIoT system (October 2022). More specifically, a 2022 survey by Microsoft identified securing the operational technology network (43%) and securing the cloud (41%) as top technical issues.
In an interview recorded on June 2023, Padraic Harrington of Forrester raised concerns over the issues that legacy IoT devices aggravate.
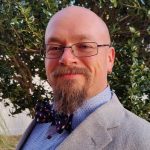
“The problem we find in the business world is that IoT ranges from things that just got shipped in last week to stuff that they’ve had in place 10–15, sometimes even 20 years…We’re not reducing the amount of IoT devices, we just keep adding in more and more and it’s just compounding the problems that already exist now.” —Padraic Harrington, Forrester
To protect sensitive data and assets, a reliable IIoT solution will require solid security and monitoring measures. Here are some recommendations from Amazon:
- Establish centralized security policies and perform regular audits on all the IIoT components—including sensors, edge gateways, and networks—to identify vulnerabilities.
- Divide your IoT network into smaller groups of components. This approach (named microsegmentation) enables to isolate workloads from each other, reducing the potential scope of a cyberattack.
- Safeguard your IIoT platform with activity monitoring, risk analytics, security information and event management (SIEM), encrypted data exchange, identity and access management (IAM), as well as network segmentation through virtual private networks.
- Ensure safer communication between IIoT platform and edge devices through data exchange standards and protocols designed to strengthen security. These encompass the OPC Unified Architecture, along with CIP Security, Modbus Secure, and more.
- Define a disaster recovery plan and update it based on security incidents. This may include reliance on cloud services to ensure data backup and business continuity.
You may also look into distributed ledger technology (DLT) to protect IoT data and identify the level of trust for your devices on the edge. Read our article to learn how Linux Foundation’s Project Alvarium records what happens to telemetry data on the way from devices to apps and sets immutable trust scores based on this historical information.
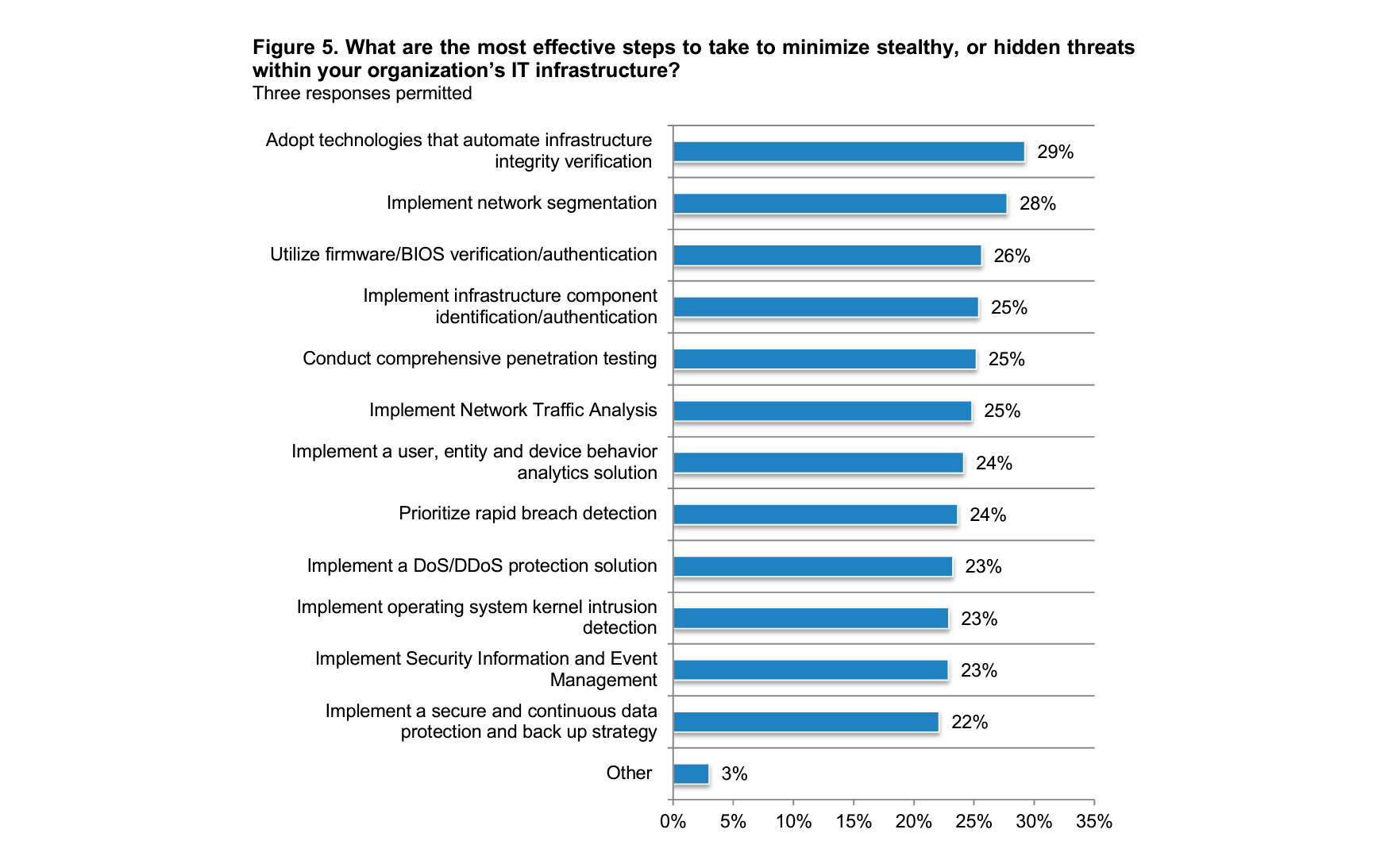
4. Overall complexity
The adoption and the progress of IIoT programs can also be hampered by the overall complexity—including technology dependencies, inefficient/outdated workflows, existing spaghetti code, time constraints, technical debt, etc. Therefore, manufacturers should consider IIoT as a strategical, transformational initiative impacting multiple business processes across the organization.
- Use case identification. McKinsey highlights that you should be ready to prioritize IIoT use cases that are likely to ensure the maximum ROI in the shortest period of time. For example, you may target essential business functions suffering from major inefficiencies. Or, start with noncritical processes presenting an opportunity of fast implementation, and then scale as these scenarios succeed. Besides, consider the expertise and resources required for such use cases, along with their scalability and replication potential across multiple locations to foster digital transformation with IoT.
- Phased rollout. To mitigate IoT scaling problems, McKinsey recommends a phased deployment across multiple waves. The rollout should be carefully planned by setting up a suitable IIoT implementation roadmap to define use cases, timeline, and responsibilities. The first results of the pilot use cases can be observed within 6–8 weeks, enabling to collect feedback from initial deployments and adjust the adoption plan.
- Change management. To better deal with the transformations triggered by new IIoT initiatives, manufacturers will need a change management strategy. First, you should establish a center of excellence to coordinate IIoT scaling. It is also recommended to promote cross-team collaboration, invest in upskilling, and involve on-site professionals to ask for their feedback. Another best practice is the identification of the operational changes required to integrate IoT into your workflows.
- A modular approach. When scaling your operations, consider creating multiple, interconnected components (one for each business function, for example) instead of expanding a single digital twin. According to Dr. Emile Glorieux of the Manufacturing Technology Center, a modular system can help you to address potential failures, facilitate maintenance, and scale IIoT by adding new subparts. “Keep things modular and scale up in a way that you don’t have a single point of failure in your system,” Dr. Glorieux suggests.
- No-code/low-code systems. A 2022 survey by PwC suggests that low-code platforms can act as accelerators for IIoT implementation and scaling. These development environments provide visual tools to facilitate coding, minimizing programming efforts. In this regard, Mendix reported that 41% of manufacturers surveyed in June 2022 want low-code systems to integrate with shop-floor devices and systems, while 39% aim to connect with legacy systems. 43% of the respondents expect low-code platforms to provide manufacturing-oriented app templates.
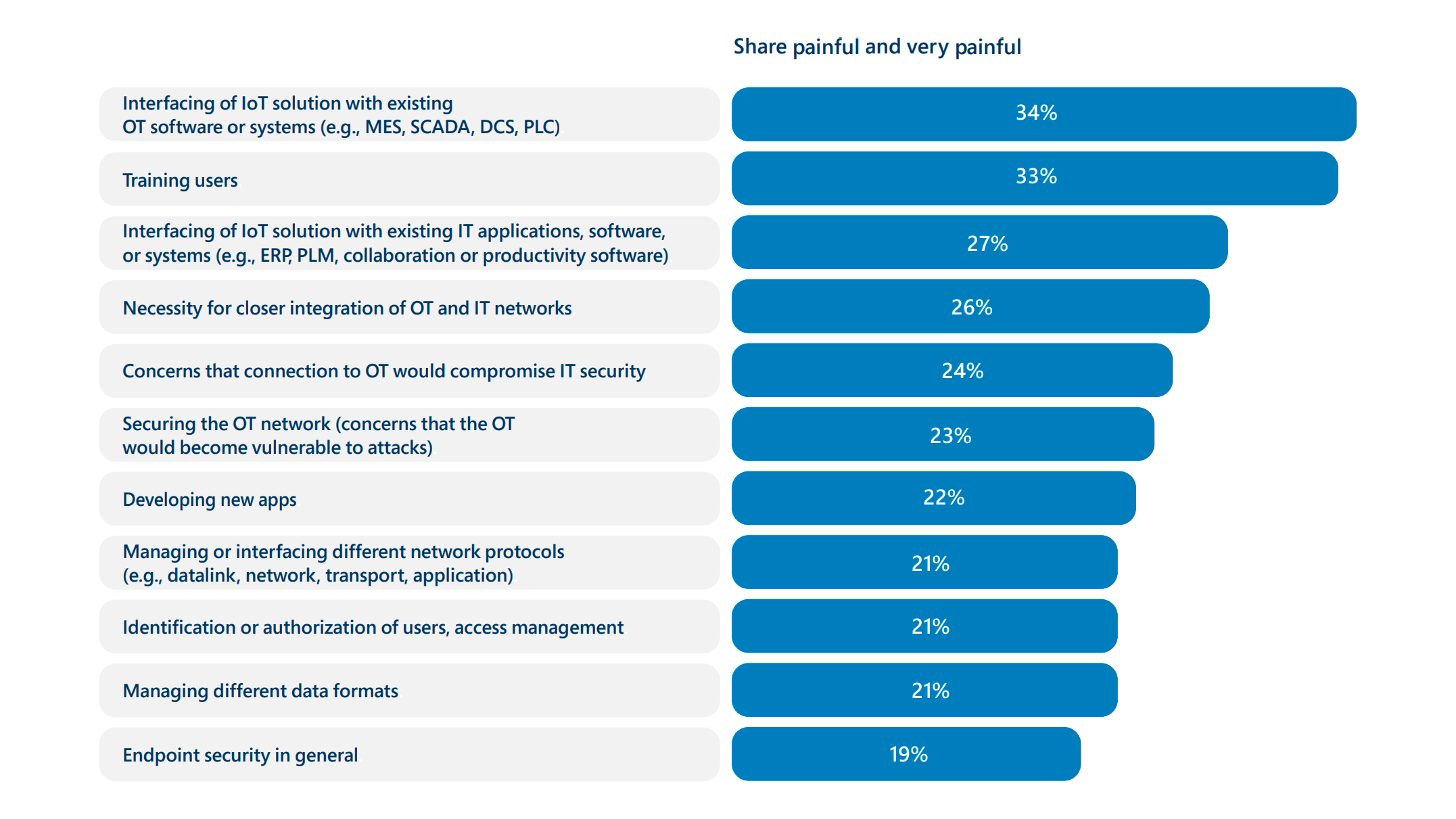
David Goeckeler, CEO at Western Digital, shared some strategic advice on managing IIoT adoption in a podcast organized by McKinsey.
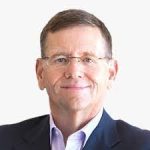
“Once you get some momentum going, it’s easier to keep it going and build faster and more of it. So, workforce engagement, infrastructure readiness, and then start with some prioritized use cases. Start small but think big. And then scale as fast as you can.” —David Goeckeler, Western Digital
Buy vs. build from scratch vs. integrate
When deciding to adopt industrial IoT, companies have a choice between building, buying, or buying and integrating a solution. In its 2023 survey, Microsoft outlined the major reasons for choosing each approach.
The main scenarios for choosing a BUILD approach are related to smart operations (54%). Specific examples include production planning/scheduling (67%), AI and machine vision-based quality control (54%), as well as remote asset monitoring and maintenance (53%). Additionally, 96% of respondents mentioned the need to meet a specific nonstandard requirement as a reason for choosing to build a solution from scratch.
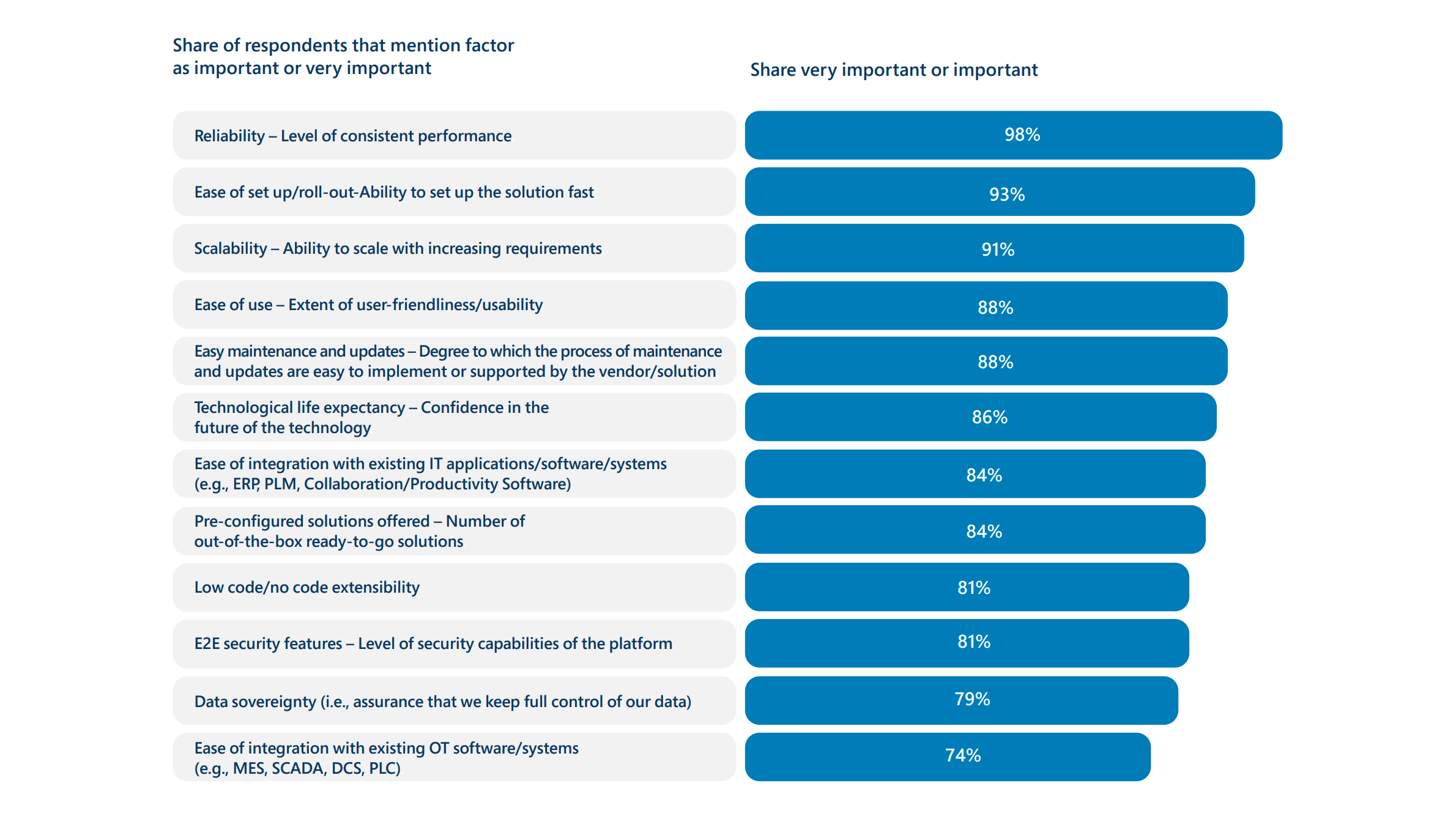
For connected products offered by manufacturers, 100% of over-the-air software updates are also done via a custom-built model, as well as integrating preconfigured APIs or interfaces into the solution (80%).
For connected products, the top three features implemented via the BUY-AND-INTEGRATE approach are condition or health monitoring (62%), performance twin (60%), and IoT data-based product usage optimization (50%).
Manufacturers that opt for the BUY route do so for footprint optimization (27%) and plant/operations network optimization (30%) scenarios. One of the main advantages of this approach is its relatively short break-even time of 12 months.
At the same time, missing capabilities for the end-user is the most cited challenge when applying this model (30%), as well as inability to tackle cyberthreats (20%).
Prioritized POCs, allies, and a plan
Fostered by a reduction in sensor and data storage costs, the industrial IoT has made great strides in manufacturing. However, when it comes to deploying and scaling IIoT, you’ll need to deal with a mix of protocols, integration issues, data silos, security gaps, system complexity, time constraints, as well as the lack of resources or specific expertise.
Still, you can overcome IIoT implementation challenges with a solid adoption strategy, POCs, KPIs, upskilling investments, and support from partners. According to a Deloitte study, 61% of organizations partner with specialized technology companies to implement smart manufacturing. In particular, approximately 50% of manufacturers are working with strategy consultants or service integrators, or both, according to a 2023 study by ISG. The report notes that multiple partners are needed to achieve smart manufacturing targets.
Starting small and then scaling where ROI seems to be positive will help you reap the benefits of industrial IoT beyond a proof of concept.
Frequently asked questions (FAQ)
-
Which IIoT scenarios are the most beneficial for manufacturing?
According to Microsoft’s 2022 survey, the vast majority of manufacturers adopt IIoT for operational improvements, such as equipment effectiveness. IIoT devices and sensors can be used for managing assets, monitoring equipment, tracking energy consumption, etc. Companies can then use this data to identify bottlenecks, enable predictive maintenance, and improve safety, resulting in higher productivity and less downtime. IIoT can also help with inventory management and location tracking, as well as lead to lower energy consumption in some cases.
-
What are the main challenges for adopting IIoT?
Besides integrating numerous systems such as SCADA, MES, PLM, ERP, etc., it can be difficult to bridge a myriad of devices that use different data formats and communication protocols. Data management is also an issue, with hundreds/thousands of sensors generating information in real time and information silos in place. Furthermore, manufacturers need to keep their existing devices updated to prevent vulnerabilities and ensure that new ones do not compromise security. Overall system complexity adds more issues to address on a large scale.
-
What security risks may come from IIoT devices?
As the number of IIoT devices grows, this creates additional points of vulnerability, especially if sensors/products are not set up and managed correctly. Microsoft warns companies that attackers may use a vulnerable device that was not isolated from the main network as an entry point. That could allow malicious actors to intercept traffic and infect other parts of the infrastructure. Legacy devices aggravate these issues.
-
How long does it take to implement an IIoT system?
Microsoft’s research indicates that the median time to build a POC of an IIoT system, get the first results, and collect initial feedback is about 6 months (2022). For a pilot rollout, the median time is around 7 more months, and a full production deployment may require about 9 months on top of that. ISG discovered that 81% of companies managed to get the first tangible results within 12 months.
-
So, develop an IIoT system from scratch or buy one?
According to another Microsoft’s survey (2023), companies mostly go with customly built IIoT solutions for smart operations, over-the-air product updates, API integration, etc. On the other hand, organizations buy off-the-shelf IIoT products for sustainability footprint and plant/operations network optimization. For smart supply chains, companies often choose to combine both approaches, buying an IIoT product, customizing it, and integrating with existing software.
Want more? Watch the video!
In this video, Paddy Harrington of Forrester Research discusses the findings from the 2023 State of IoT Security report.
Further reading
- A Collection of 20+ MQTT Broker Performance Benchmarks (2020–2023)
- LF’s Project Alvarium: Ensuring Trusted IoT Data at the Edge with DLT
with contributions from Yaroslav Goortovoi.
Subscribe to new posts
Contact us and get a quote within 24 hours
